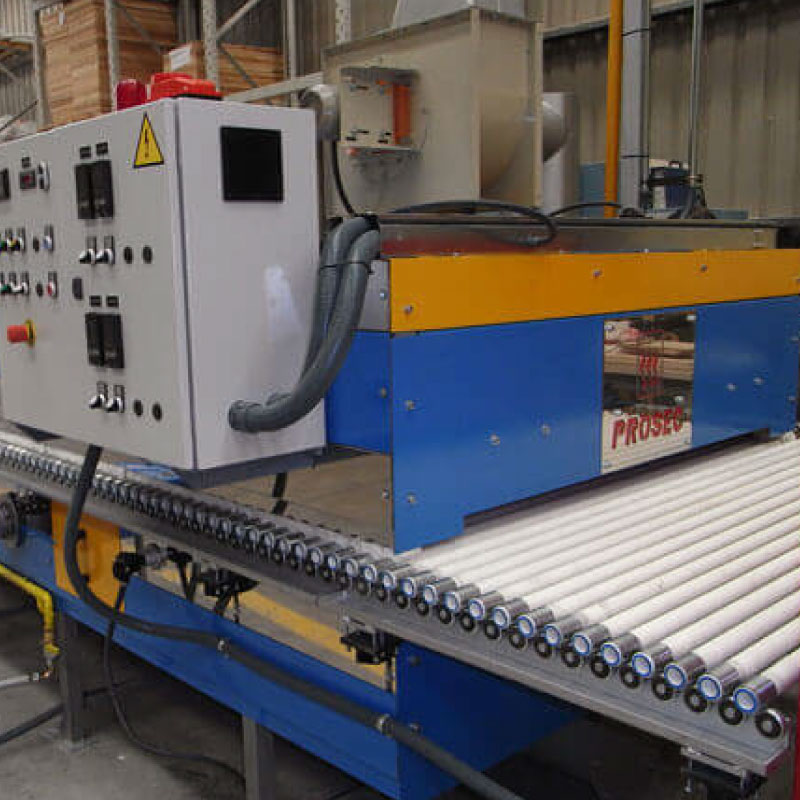
En el competitivo mundo de la cerámica, PROSEC ofrece soluciones avanzadas de ingeniería para el secado y la cocción, destacando su experiencia en el fraguado en Villa Real para pavimentos, revestimientos, cerámicas estructurales esmaltadas y piedra natural. Nuestra misión es proporcionar equipos de alto rendimiento que maximicen la eficiencia productiva, optimizando cada etapa del proceso y adaptándonos a los retos específicos de cada planta cerámica.
Experiencia y compromiso con la calidad
Especializados en la fabricación de Kiln, Dryer y equipos para aplicaciones especiales, en PROSEC diseñamos soluciones personalizadas para cubrir las necesidades concretas de nuestros clientes, manteniendo un compromiso constante con la calidad. Además, ofrecemos servicios de modificaciones, reparaciones y mantenimiento, prolongando la vida útil de los equipos y reduciendo costes de operación gracias a un servicio postventa en Villa Real profesional y ágil.
Nuestro equipo de expertos colabora estrechamente con cada cliente para analizar sus líneas de producción y proponer mejoras que incrementen la productividad y garanticen un fraguado en Villa Real uniforme y de alta calidad, asegurando que cada pieza cumpla con los estándares más exigentes del mercado cerámico.
Asistencia técnica y servicio postventa en Villa Real
En PROSEC entendemos que un equipo de calidad necesita un soporte integral. Por eso, nuestro servicio postventa en Villa Real no termina con la entrega de los equipos; acompañamos al cliente en cada etapa de la explotación, ofreciendo asistencia técnica especializada para mantener la continuidad y estabilidad del proceso productivo. Este enfoque garantiza que las plantas cerámicas puedan adaptarse rápidamente a cambios en la demanda, optimizando recursos y asegurando procesos rentables y sostenibles.
Nuestro compromiso con la tecnología avanzada nos permite aplicar conceptos innovadores en cada proyecto, desarrollando líneas de equipos que colocan a nuestros clientes un paso adelante en el mercado global.
Horno multifuncional en Villa Real eficiencia y fiabilidad
Con nuestros hornos multifuncionales en Villa Real, es posible alcanzar la plena producción en tan solo dos horas de calentamiento, reduciendo significativamente los tiempos de parada y arranque, y logrando procesos estables, fiables y con menor consumo energético. Estas características se traducen en una mayor capacidad de producción y en un ahorro considerable en costes de mantenimiento y operación.
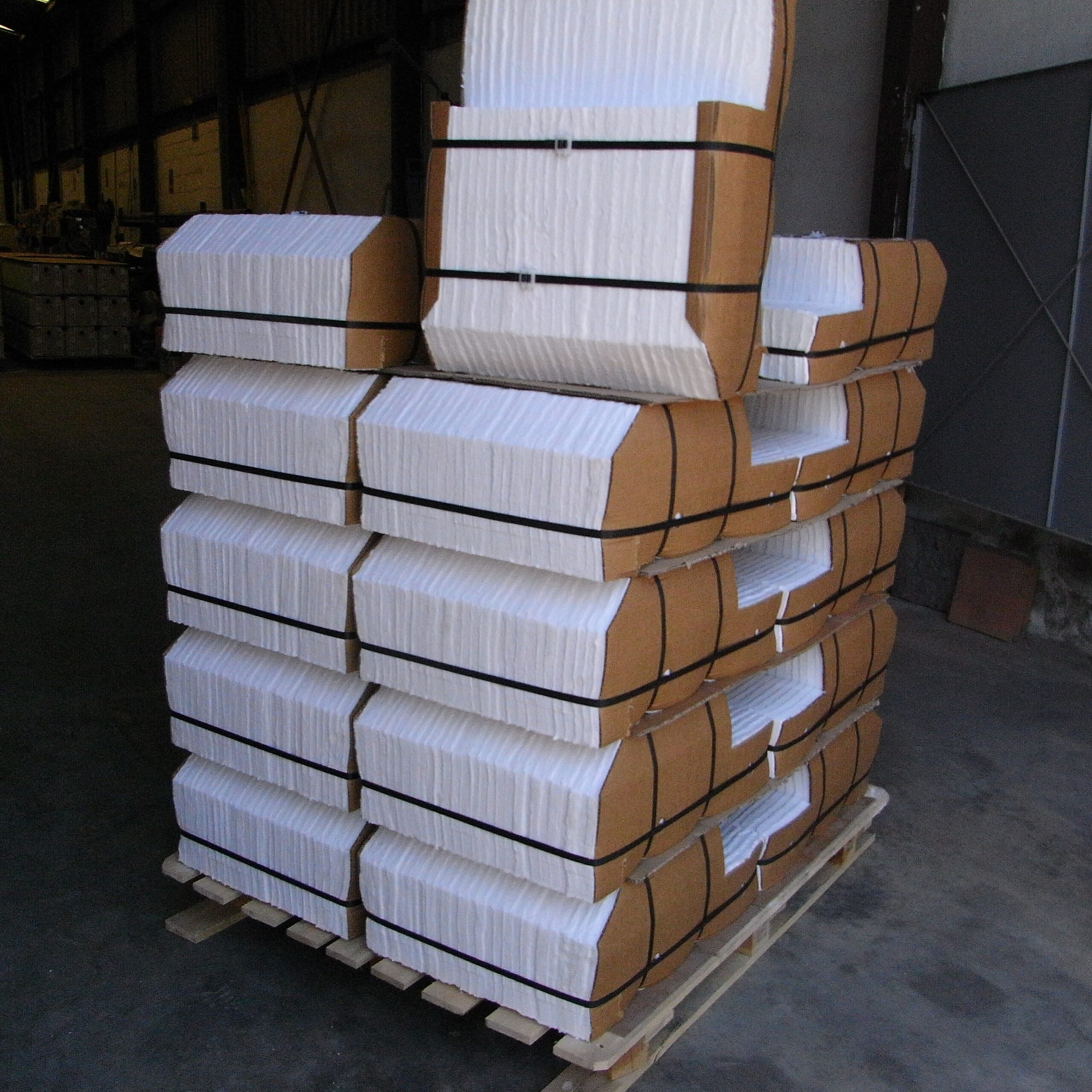